Bradbury Group Customer Service
To be the most trusted and preferred supplier in the global markets we serve.
+1.620.345.6394
BRADBURY TECHNICAL SUPPORT TEAM
Call +1.620.345.6394.
Ask for customer Service!
HELPING YOU GET WHAT YOU WANT, NEED, AND EXPECT.
The Bradbury Group is committed to providing you with world-class customer service through our Technical Service Departments. Our knowledgeable staff has many years of service in the metal processing industry and is ready to assist you with your spare parts needs, service contracts, and technical questions. The Bradbury Group utilizes the latest technology in remote diagnostics to ensure our customers are supported in a timely fashion minimizing down-time.
We offer Controls Upgrades, e-Drive Upgrades, Roll Tooling & Recuts, Preventative Maintenance Agreements, Operator Training, Spare Parts Inventory Planning and much more!
Contact Customer Service
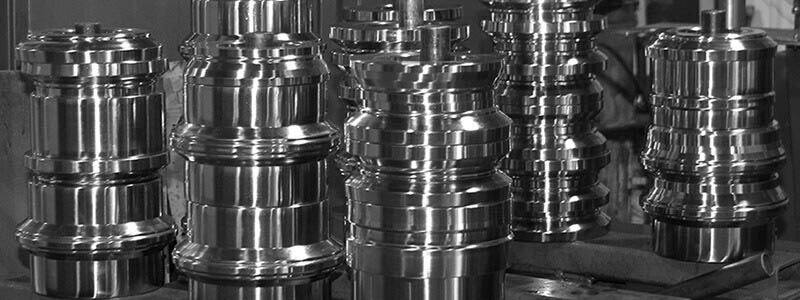